Over the course of his undergraduate career, Bacogeorge built an automated vibrating-sample magnetometer. The device will advance current and future physics research into magnetic polymers, Professor Ben Evans says.
It began with a tap on the shoulder and a leap of faith in Stratton Bacogeorge’s ’22 first year at Elon.
Bit by bit over the next three years, he engineered and built an automated vibrating-sample magnetometer. When he graduates with his B.S. in engineering later this month, he’ll leave behind an instrument that characterizes magnetic polymers by vibrating them rapidly, inducing a current through a magnetic field, and recording their reactions.
Bacogeorge’s magnetometer furthers the capabilities of Elon’s physics research. Current projects — examining the potential to disinfect medical implants without surgery through magnetic induction and understanding the magnetic properties of metals encased in soft materials — as well as future ones will benefit from the device.
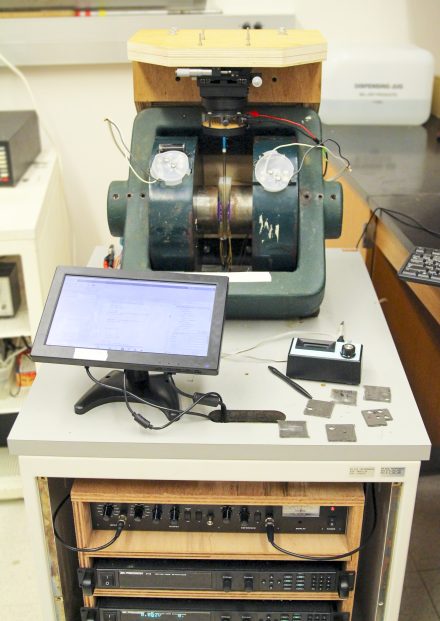
“This is an important tool for a magnetics workshop, where you need to be able to characterize the responses of a material to a magnetic field. There are a lot of projects this will advance,” said Professor of Physics Benjamin Evans. “This magnetometer allows us to obtain the magnetic characterization we need for publications and materials design.”
Commercial magnetometers start at about $150,000. Relying on grit and ingenuity, Bacogeorge built one for about $7,000 with funds from a National Science Foundation grant Evans was awarded in 2017 and from Evans’ T.E. Powell Jr. professorship. The device approaches 1 Tesla of intensity — or one newton of force per ampere of current per meter of conductor. For comparison, a strong refrigerator magnet produces about 0.01 T, so the magnet in the lab is 100 times stronger.
The project began in an after-class conversation during Bacogeorge’s first year. Enrolled in Evans’ section of General Physics II, he was drawn to the professor’s good humor and investment in the material. As Evans learned of Bacogeorge’s interest in engineering, he pitched the project: “If I gave you a magnet to get started, do you think you could engineer it?,” he asked Bacogeorge.
It soon became Bacogeorge’s hobby: learning the physics behind magnets and magnetic fields, reading papers about how vibrating-sample magnetometers work, procuring necessary parts and writing software to operate the system and automate data collection. Spare hours were spent in the physics lab, working with a large, ancient-looking magnet previously gathering dust in a corner of McMichael Science Center.
“The first year was devoted to learning the actual physics behind it. I really was in over my head,” Bacogeorge said. “I was not sure I was doing but I could see an end goal.”
Bacogeorge met often with Evans, who advised him and procured additional materials. Presentations at the National Conferences on Undergraduate Research and Elon’s Spring Undergraduate Research Forum followed in his sophomore and junior years. This year, the project became a for-credit independent research course, allowing time and structure to complete the magnetometer.
“Working with Dr. Evans, I’m like an engineer working under my supervisor, reporting back to him weekly,” Bacogeorge said. “This year has been focused on signal detection, designing the pickup coils themselves and having the whole system communicate as one unit. Before I graduate, I want to be able to get a complete sample hysteresis curve, which is the characterization we’re looking for when we test a sample.”
“Stratton is an engineer,” Evans said. “He finds a project or something that needs to be accomplished, and he figures out how to do it. That independence was there right from the start.”
In addition to the magnetometer research, Bacogeorge was a member of a team of seniors who researched the use of Raman laser spectroscopy in identifying surface defects on silicon carbide wafers as part of the Senior Engineering Design Capstone Project. Those wafers are used as semiconductors in microchips that power electronic devices. Defects in the wafer surface can cause devices to malfunction. The project was sponsored by Wolfspeed of Durham.
Following graduation, Bacogeorge has accepted a position in Wastequip’s Engineering Leadership Development Program. He will spend the next several years learning various aspects of the Charlotte-based waste handling equipment manufacturing business. He joins engineering alumnus Matthew Del Valle ’21 in the company’s engineering leadership program.
“When I was a first-year student, I could not have seen myself doing physics research. Now I’m deep into magnetics physics research,” Bacogeorge said. “It’s very cool to leave something behind at Elon.”